Autonomous cars are making headlines, but what about using automated platooning technology for truck fleets or the military? The technology may be able to cut fuel costs and allow for the driverless transport of goods through dangerous areas.
By Karl Vilacoba
They moved with the precision of racecars hugging tight turns in close synchronization to cut down on air resistance. But there was no racetrack, just a Nevada interstate, and in this case the vehicles weren’t racecars, but a pair of 18-wheelers.
When the driver in the front truck sped up or tapped on the brakes for a passing car, the rear truck responded instantly. But the driver in the trailing truck wasn’t accelerating or braking, that work was being done for him. All he had to do was steer.
The trucks were outfitted with a system designed by Silicon Valley-based Peloton Technology that the company says can yield major fuel savings and improve driver safety. Peloton’s automated platooning technology makes it possible for big rigs to emulate what NASCAR drivers call “drafting.” When one vehicle closely tails another at highway speeds, the lead car bores through the air and relieves the car behind it of some of the air resistance. At the same time, the second car absorbs a portion of the rear drag for the lead car. When the cars operate together as a team, they can drive faster while burning less fuel than they would on their own.
Peloton has been piloting the technology with two- and three-truck convoys and plans to keep the sample size small for the foreseeable future. However, Lockheed Martin has tested similar technology for the military, and the results show the technology could be used for larger platoons in certain settings.
Peloton’s research has found that at a 40-foot distance between trucks, the front vehicle cuts down fuel consumption by 5 percent and the rear cuts it by 10 percent, according to Chuck Price, Peloton’s vice president of engineering. Add a third middle vehicle to the mix and its fuel would drop 15 percent, he said. When you consider that individual carriers can burn $100,000 per year of diesel, automated platooning may be an appealing option to a company with a large fleet.
“We’re talking about very big money here,” Price said.
And it can get even bigger. The closer the trucks platoon together, the greater the fuel savings. Peloton (the French word for “platoon”) has successfully tested automated convoys as close as 10 feet apart, but for the sake of public acceptance and making drivers feel safe, that’s not an approach likely to be used on public roads any time soon.
“We’ve found that the sweet spot for both driver comfort and efficiency is 40 feet,” Price said. “At that distance, the rear driver starts to see the pavement between them, not just the rear [of the other truck].”
Peloton believes that its automated platooning system is not only road safe, but safer than manual human driving. The system’s combination of radar, GPS, video and automatic braking technologies eliminate the kind of human errors that can befall drivers after long hours on the road, Price said. At the same time, a network operations center owned by the company would monitor each automated convoy and relay important real-time information about traffic, weather and road emergencies to drivers.
Automated Supply Lines
While computerized driving technologies are under exploration by multiple automakers and even Google, Peloton has no direct competitor in the automated truck platoon business at the moment. Lockheed Martin and Volvo, which have conducted their own tests on automated convoys, are now among Peloton’s major investors.
However, Lockheed Martin has made substantial progress on its military version of the concept and continues to develop it in parallel with the commercial program. With its system, soldiers trucking supplies through hot zones in places like Afghanistan and Iraq would no longer be vulnerable to roadside IEDs or armed checkpoints run by hostile parties.
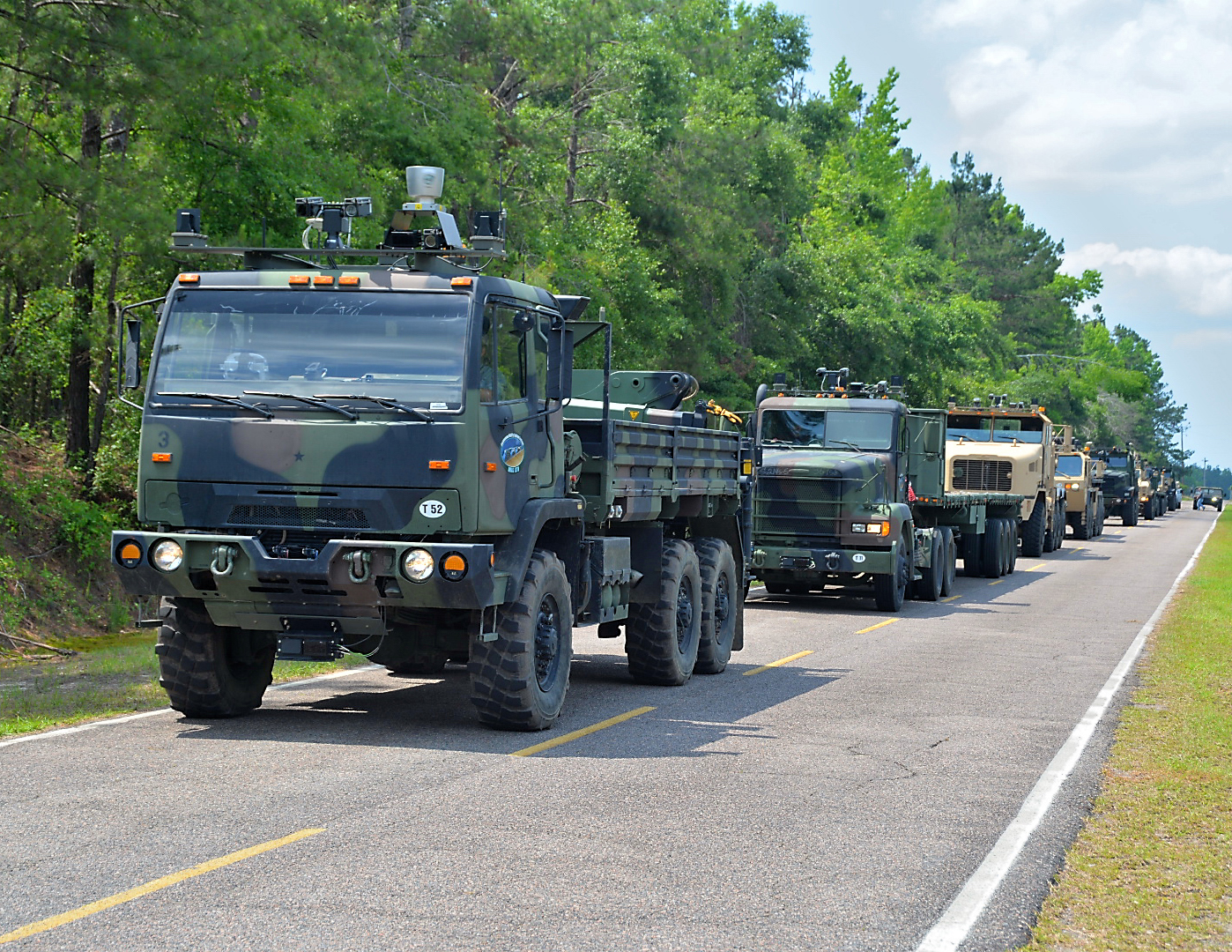
Last year, Lockheed Martin successfully demonstrated a fully driverless convoy of seven trucks at 40 miles per hour with its Autonomous Mobility Appliqué System (AMAS) at a facility in South Carolina. A few months earlier, driverless vehicles equipped with the AMAS system navigated obstacles such as road intersections, oncoming traffic, stalled and passing vehicles, pedestrians and traffic circles in simulated environments on a military base in Fort Hood, Texas. In contrast, the planned protocol for drivers using Peloton’s system is to disengage from the autonomous system and take full control of the trucks the moment they enter an urban area.
Why wouldn’t a company that seems to have all the answers – along with ample capital -- just go it alone? According to Lockheed Martin spokesman John Kent, the company takes the view that the military and civilian applications are two distinct technologies with separate purposes.
“Peloton’s capability is focused on manned commercial truck platooning operation on public highways and will provide improved fuel economy of platooned fleets at low cost and low risk,” he said. “The Peloton system assists an active driver with longitudinal control during periods the system is linked. Lockheed Martin’s capability has been designed to meet military operations in unstructured environments and is fully autonomous. The missions are very different.”
AMAS convoys haven’t yet been deployed in a live military setting. However, Lockheed Martin’s driverless Squad Mission Support System vehicle, which uses a similar software system as AMAS, was used in Afghanistan in 2012, Kent said.
The Future of Trucking?
The Peloton system, on the other hand, had already logged 16,000 miles on America’s roads at the time of this writing. Public demonstrations have been done on live roads in Michigan, Florida, Nevada and Utah, with trials upcoming in Texas and California. “It’s real,” Price assures.
The trucking community has taken notice. American Trucking Association (ATA) Director of Engineering Ted Scott said his organization holds a neutral position on platooning technologies, but is monitoring their advancement closely.
If autonomous vehicle technologies logically promise to make driving an endangered activity in the long term, the implications would seem especially threatening for the trucking industry. Automated platooning technology could potentially make a convoy of trucks duplicate the work of freight trains, with a long line of unmanned vehicles carrying crude from the Bakken region to a refinery in New Jersey or Texas.
Not so fast, according to Scott. While acknowledging that platooning could logically be seen as “a baby step to autonomous or robotic trucking,” he said there are reasons why something like that won’t happen anytime soon, if ever.
First, although the public may eventually come around to the idea of sharing the road with self-controlled cars, he doubts people will be as accepting with massive unmanned tractor trailers, especially in city traffic.
And from a business perspective, Scott believes platooning only makes sense in limited situations – namely, for larger companies with multiple trucks heading from the exact same starting point to the same destination. Because the rear truck sees greater fuel savings than the lead one, he wondered if disputes over the time split could make mixed companies reluctant to enter into joint platooning arrangements.
To date, state governments have been supportive. Utah recently passed legislation to accommodate the technology while other states are in the process of doing the same, Price said. Some officials see automated platooning as a practice that could help relieve congestion and provide economic benefits, he said.
For its part, Peloton is aware of the sort of trepidation the public may initially harbor and is therefore planning to ease its technology on to American roads with measures that will make people more comfortable. A driver will remain behind the wheel and steer the automated rear vehicles, and convoys will extend no longer than two vehicles, even though the technology has already demonstrated it can handle more.
“We want the public to understand it and accept it,” Price said.
Karl Vilacoba is a freelance writer based in New Jersey. This article appeared in the Winter 2016 Edition of InTransition Magazine.
FULL STORY: Automated Systems Seen as a Means for Cutting Fuel Consumption and Improving Road Safety
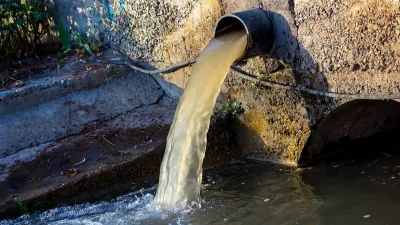
Alabama: Trump Terminates Settlements for Black Communities Harmed By Raw Sewage
Trump deemed the landmark civil rights agreement “illegal DEI and environmental justice policy.”

Planetizen Federal Action Tracker
A weekly monitor of how Trump’s orders and actions are impacting planners and planning in America.

The 120 Year Old Tiny Home Villages That Sheltered San Francisco’s Earthquake Refugees
More than a century ago, San Francisco mobilized to house thousands of residents displaced by the 1906 earthquake. Could their strategy offer a model for the present?
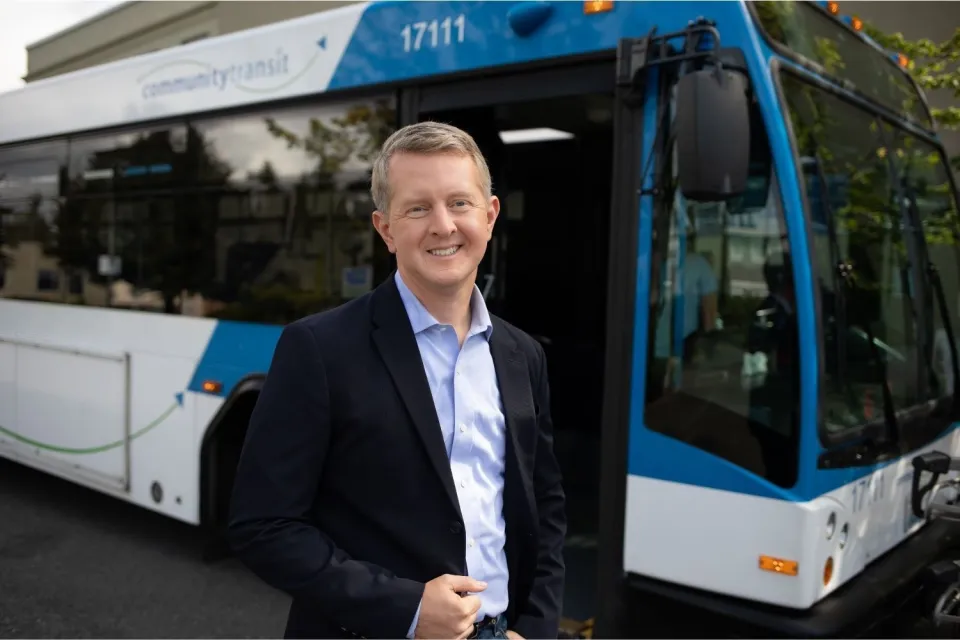
Ken Jennings Launches Transit Web Series
The Jeopardy champ wants you to ride public transit.
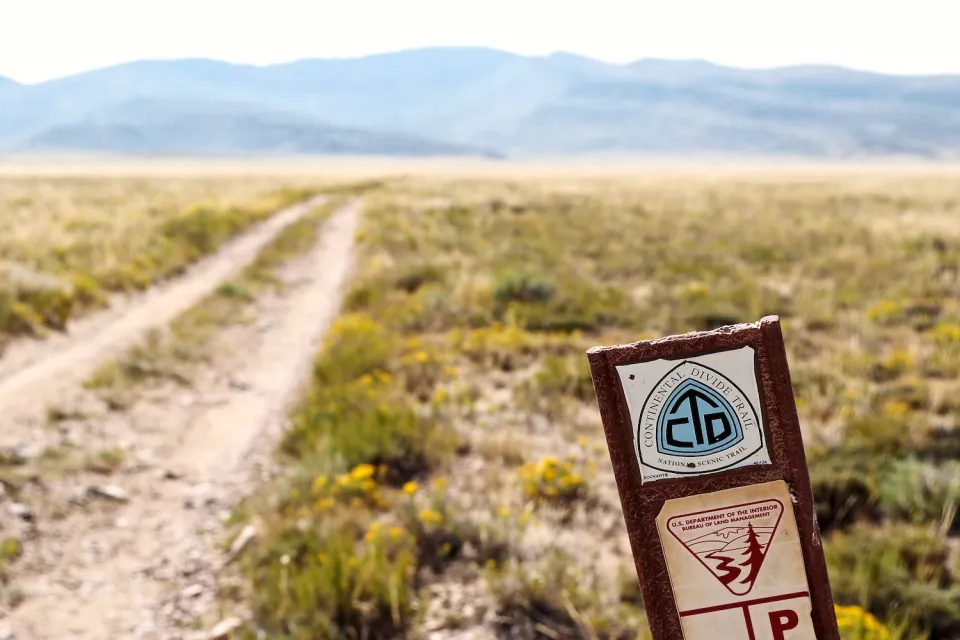
BLM To Rescind Public Lands Rule
The change will downgrade conservation, once again putting federal land at risk for mining and other extractive uses.

Indy Neighborhood Group Builds Temporary Multi-Use Path
Community members, aided in part by funding from the city, repurposed a vehicle lane to create a protected bike and pedestrian path for the summer season.
Urban Design for Planners 1: Software Tools
This six-course series explores essential urban design concepts using open source software and equips planners with the tools they need to participate fully in the urban design process.
Planning for Universal Design
Learn the tools for implementing Universal Design in planning regulations.
Clanton & Associates, Inc.
Jessamine County Fiscal Court
Institute for Housing and Urban Development Studies (IHS)
City of Grandview
Harvard GSD Executive Education
Toledo-Lucas County Plan Commissions
Salt Lake City
NYU Wagner Graduate School of Public Service