To improve housing costs and economic conditions at once, look to the locations of modular housing factories.
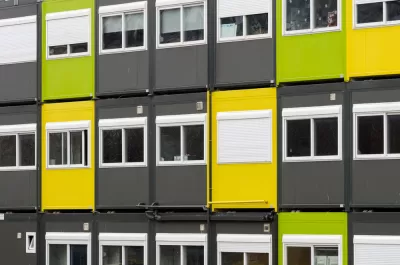
Affordable housing developers are keenly aware of the growing need to house struggling residents quickly. The pandemic has only exacerbated the mismatch between housing supply and housing need. There is, of course, also an economic crisis, and affordable housing development is a proven strategy to spur job creation and spark positive ripple effects across multiple sectors.
However, operational challenges precipitated by the pandemic—not to mention the strain on public resources‚ have made affordable housing developers extremely sensitive to the costs of building new developments. This has increased the appeal of modular housing construction, which has been promoted as a way to boost productivity, cut costs, and force innovation in traditional construction. Modular homes are residences built to near completion in factory environments, and later transported in sections to construction sites.
However, that potential has not yet been realized, and one of the reasons is the expense and delay that comes from shipping the modular parts in from distant factories. If components of a modular home are built at a local factory situated nearer the construction site, developers have the convenience of both logistical and cost efficiencies, cutting down project time and contributing to a smaller carbon footprint.
A strategy that would address housing supply, construction cost, job creation—and even the jobs-housing mismatch—would be to locate more modular housing factories directly in regions with high housing costs, in parts of those regions that suffer from lack of jobs and long commutes to what jobs there are. Developers seek certainty in the building environment, and a robust set of local fabrication facilities could bring efficiency, reliability, and timely delivery.
Take Southern California, for example. The Southern California Association of Governments (SCAG), the metropolitan planning organization for the region, has been told by the state housing department that the region will need ...
FULL STORY: Build Modular Housing Factories Near Areas with High Housing Costs
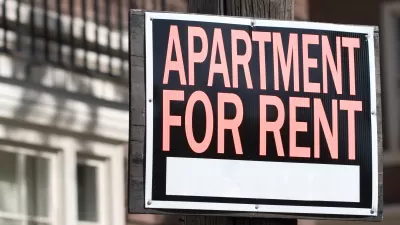
Trump Administration Could Effectively End Housing Voucher Program
Federal officials are eyeing major cuts to the Section 8 program that helps millions of low-income households pay rent.

Planetizen Federal Action Tracker
A weekly monitor of how Trump’s orders and actions are impacting planners and planning in America.

Ken Jennings Launches Transit Web Series
The Jeopardy champ wants you to ride public transit.

Washington Legislature Passes Rent Increase Cap
A bill that caps rent increases at 7 percent plus inflation is headed to the governor’s desk.
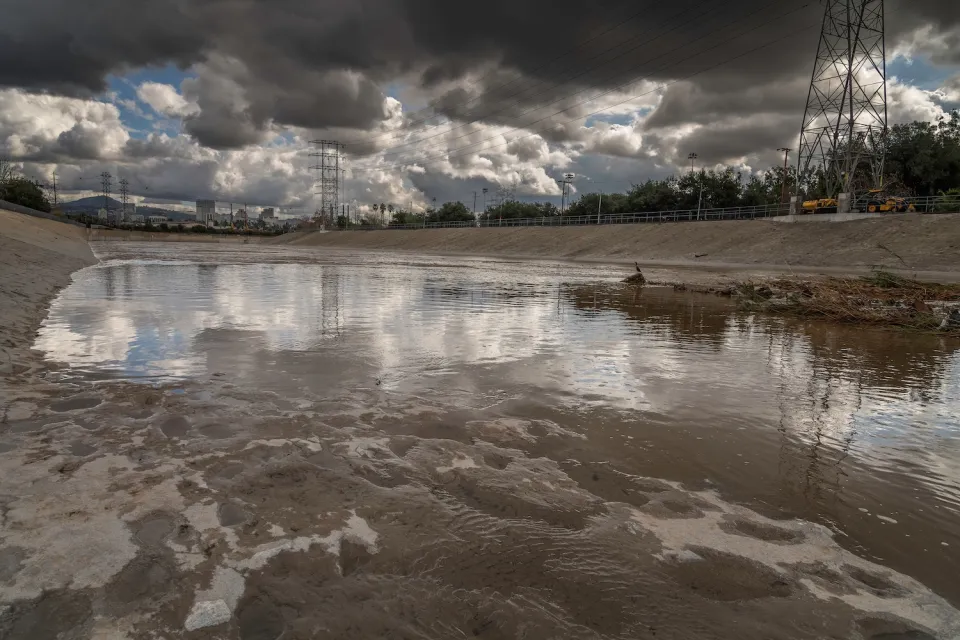
From Planning to Action: How LA County Is Rethinking Climate Resilience
Chief Sustainability Officer Rita Kampalath outlines the County’s shift from planning to implementation in its climate resilience efforts, emphasizing cross-departmental coordination, updated recovery strategies, and the need for flexible funding.
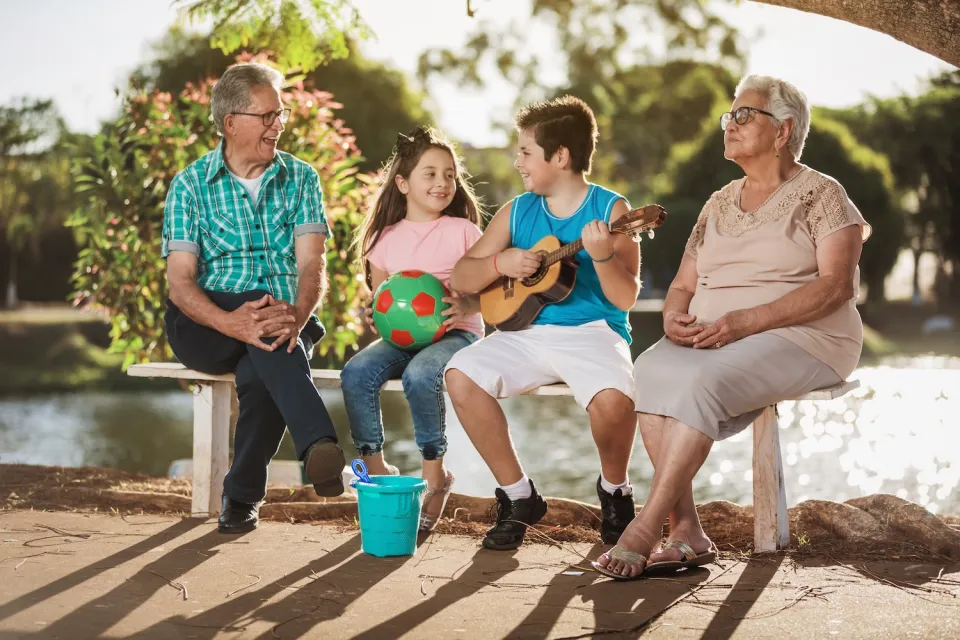
New Mexico Aging Department Commits to Helping Seniors Age ‘In Place’ and ‘Autonomously’ in New Draft Plan
As New Mexico’s population of seniors continues to grow, the state’s aging department is proposing expanded initiatives to help seniors maintain their autonomy while also supporting family caregivers.
Urban Design for Planners 1: Software Tools
This six-course series explores essential urban design concepts using open source software and equips planners with the tools they need to participate fully in the urban design process.
Planning for Universal Design
Learn the tools for implementing Universal Design in planning regulations.
Heyer Gruel & Associates PA
Ada County Highway District
Institute for Housing and Urban Development Studies (IHS)
City of Grandview
Harvard GSD Executive Education
Toledo-Lucas County Plan Commissions
Salt Lake City
NYU Wagner Graduate School of Public Service